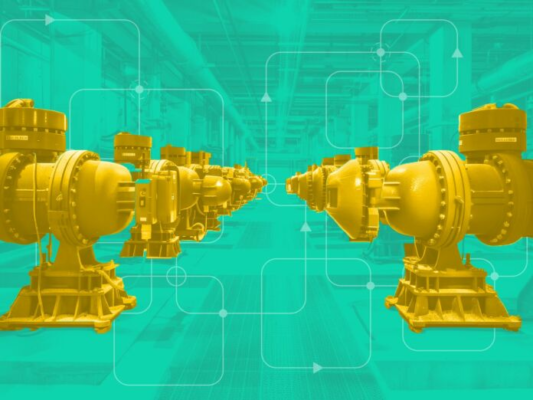

The world of industrial processes is undergoing a significant transformation with Industry 4.0, a movement integrating advanced technologies like the Internet of Things (IoT), artificial intelligence (AI), and machine learning (ML) to build smarter, more efficient systems.
At the heart of many industrial applications, pumps are evolving from simple mechanical devices to intelligent systems, leveraging real-time data and predictive analytics for optimized performance and cost savings. Here, we explore how IoT and Industry 4.0 technologies are reshaping the future of pumps across sectors such as water management, oil and gas, and manufacturing.
Understanding the Revolution of Industry 4.0
Industry 4.0, also known as the Fourth Industrial Revolution, integrates automation, data processing, and connectivity to enable smart manufacturing. With IoT as a fundamental driver, Industry 4.0 enables equipment to communicate, share insights, and optimize performance with minimal human intervention. This evolution marks a shift from traditional reactive maintenance to proactive, data-driven strategies, promising unprecedented operational efficiency and innovation across industries.
The Role of IoT in Industrial Automation
IoT introduces a network of connected devices that gather and exchange data to enhance automation, streamline operations, and enable predictive maintenance. For pumps, this means real-time monitoring, early detection of issues, and adjustments that maximize efficiency and prevent costly downtime. IoT-connected pumps are designed to operate smarter and extend their lifespan while conserving resources—essential in industries where pumps operate around the clock.
Why Pumps Are Critical to Industrial Infrastructure
Pumps in Key Sectors (Water, Oil, Gas, etc.)
Pumps serve as the backbone of essential industries, facilitating the movement of liquids in applications from water and wastewater treatment to oil, gas, and chemical production. The reliability of dosing pumps is crucial for these sectors to maintain operational continuity, meet regulatory requirements, and ensure safety. Therefore, adopting IoT-enabled, Industry 4.0-ready pump systems can transform how these sectors operate, enhancing both performance and compliance.
The Growing Need for Smarter Pump Systems
With rising demands for energy efficiency and environmental responsibility, there’s a pressing need for pumps that adapt to changing operational requirements. Smarter pumps can automatically adjust to fluctuating loads, making them more efficient in resource use and reducing energy consumption, which is vital for industries looking to minimize their carbon footprint.
How Industry 4.0 is Shaping the Future of Pump Technology
Real-Time Data Collection and Analysis
One of the standout benefits of Industry 4.0 is real-time data collection. IoT-enabled sensors track pressure, temperature, flow rate, and other metrics to provide continuous insights into a pump’s performance. This data is sent to cloud-based platforms, where it is analyzed to ensure the pump operates within optimal parameters.
Predictive Maintenance and Reduced Downtime
Predictive maintenance is a game-changer for pumps. By using advanced analytics, AI, and ML, IoT-connected systems can predict when a pump might fail or require maintenance. This reduces downtime, prevents catastrophic failures, and prolongs the life of the equipment, making it more cost-effective in the long run.
Enhanced Energy Efficiency and Sustainability
Sustainability is a growing priority, and IoT-driven pumps can optimize energy use through automation and continuous monitoring. These systems identify inefficiencies and make adjustments that lower energy consumption, ultimately reducing operational costs and carbon emissions. Energy-efficient pumps are not only environmentally friendly but also help industries comply with global environmental regulations.
IoT Integration in Modern Pump Systems
Smart Sensors and Real-Time Monitoring
Smart sensors are at the core of IoT-enabled pump systems. These sensors track key performance indicators like vibration, temperature, and pressure, giving operators instant feedback on the pump’s status. If the system detects an anomaly, it can automatically alert operators or even make adjustments to avoid system failure.
Remote Control and System Optimization
IoT enables remote monitoring and control, allowing operators to manage pumps from any location. This flexibility is invaluable, especially for industries with facilities in remote areas. With remote control, companies can optimize pump performance, troubleshoot issues, and reduce response times in emergencies.
Data-Driven Insights for Efficiency and Reliability
Data from IoT-enabled pumps is more than just numbers; it provides actionable insights for optimizing operations. Advanced data analytics can pinpoint trends and issues that may go unnoticed, helping companies adjust their processes and reduce resource consumption. These insights lead to improved reliability and efficiency, as adjustments are made before minor issues become major problems.
Benefits of IoT-Enabled Pumps for Various Industries
Cost Reduction and Resource Optimization
With IoT, companies can monitor pump performance continuously, avoiding inefficiencies that drive up costs. Data-driven insights ensure pumps operate at peak efficiency, reducing energy and maintenance costs, and optimizing the use of resources like water and electricity.
Improved Safety and Compliance
IoT-enabled pumps can enhance safety by identifying issues before they lead to failure. Continuous monitoring means that compliance with safety standards and environmental regulations is easier, as issues can be corrected before they become regulatory violations. This is especially important in industries like oil and gas, where a failure could lead to environmental harm and significant fines.
Prolonged Equipment Life
By predicting maintenance needs, IoT-enabled pumps reduce wear and tear. Regular servicing based on actual wear rather than time intervals extends equipment life, saving costs in the long run. This is particularly beneficial for industries with high equipment costs, as it allows them to maximize the lifespan of their investment.
Challenges and Solutions in Implementing IoT in Pumps
Data Privacy and Security Concerns
One of the biggest challenges with IoT adoption is ensuring data security. The more connected devices a system has, the more vulnerable it is to cyber threats. To address this, companies must invest in robust cybersecurity measures, including encryption, regular software updates, and network security protocols.
High Initial Costs and Integration Complexity
Implementing IoT technology can be costly, especially for companies upgrading legacy equipment. However, the long-term savings in maintenance and energy costs often offset these initial expenses. Companies can also consider phased adoption, starting with critical systems and expanding IoT capabilities over time.
Need for Skilled Workforce
Industry 4.0 and IoT technologies require a skilled workforce proficient in data analytics, cybersecurity, and IoT technology management. Companies may need to invest in training or hire skilled professionals to manage these systems effectively. Partnerships with tech firms specializing in IoT solutions can also bridge this gap.
The Path Ahead: Emerging Trends in Pump and IoT Technology
Artificial Intelligence and Machine Learning
AI and ML are critical for predictive maintenance and optimizing pump performance. By learning from data, these technologies enable pumps to self-correct, identify patterns, and make informed adjustments, enhancing reliability and performance over time.
Digital Twins and Virtual Simulations
A digital twin is a virtual replica of a physical pump system. It allows operators to simulate real-world scenarios and predict outcomes without affecting actual operations. Digital twins help companies test changes in a risk-free environment and streamline processes before applying them on a large scale.
Growing Focus on Sustainability
As global demand for sustainable practices rises, IoT-enabled pumps are positioned to support these initiatives. By minimizing waste and energy use, these systems help industries move towards net-zero emissions goals. The future of IoT in pump technology aligns closely with sustainability, offering companies a pathway to environmental responsibility without sacrificing productivity.
Conclusion
The integration of IoT and Industry 4.0 technologies into pump systems is transforming industries by improving efficiency, reducing costs, and enhancing sustainability. Although there are challenges, the benefits far outweigh them. As IoT-enabled pump systems continue to evolve, they will become even more intelligent, efficient, and crucial to achieving industrial goals in the coming years.
FAQs
How does IoT improve pump efficiency?
IoT improves pump efficiency by enabling real-time monitoring and data analysis, allowing pumps to self-adjust and avoid energy waste, reducing costs, and improving operational efficiency.
What is predictive maintenance, and why is it crucial for pumps?
Predictive maintenance uses data analytics to predict when a pump may require servicing, helping prevent unexpected failures and extending the pump’s lifespan.
Can IoT-enabled pumps reduce operational costs?
IoT-enabled pumps help reduce operational costs by optimizing energy use, lowering maintenance expenses, and improving resource management.
What industries benefit most from IoT in pump systems?
Industries like water management, oil and gas, and manufacturing benefit significantly from IoT-enabled pump systems due to their continuous operation and high maintenance needs.
What challenges do companies face when integrating IoT into pumps?
Challenges include data security risks, high initial costs, integration with legacy systems, and the need for a skilled workforce to manage these advanced technologies.