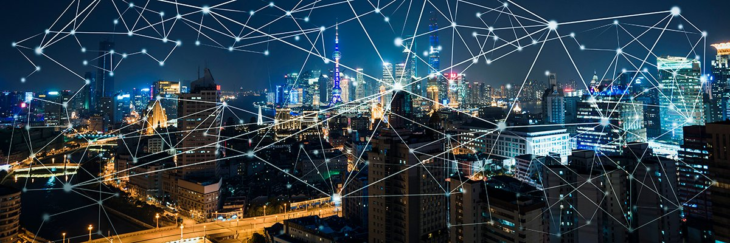
Many domains of focus within sustainable manufacturing can benefit from implementing IoT.
Manufacturers can use IoT to collect data, then convert that data to valuable business information using analytics and decision support tools. Organizations can place sensors that provide real-time data on products in the field, or on manufacturing equipment to collect performance data.
Information extracted from IoT data facilitates system-level analyses that companies can use to improve product quality, increase production efficiencies and optimize resource utilization.
Management improvement
IoT improves dashboard access to real-time operational KPIs regarding sustainability targets, such as emissions, waste and recyclable material flow, as well as energy and water use and efficiency.
Initiatives that use IoT to improve efficiency can also advance sustainable manufacturing goals because they provide access to sustainability-related data and reporting systems such as the following:
- Automated monitoring.
- Implementation of controls regarding internal and external costs.
- Supplier networks.
- Manufacturing system state.
- Compliance with sustainability initiative KPIs.
- Data reliability transparency.
Gathering network edge data from a rich selection of machine and environmental sensors allows for new opportunities in condition-based and performance-driven asset management, reducing operations risk and monitoring waste while improving efficiency.
Such use of intelligent systems for manufacturing performance modeling can also increase an organization’s competitive advantage. Real-time IoT monitoring might help strengthen a manufacturer’s reputation because it enables expedited responses to data requests and creates opportunities for companies to demonstrate system transparency, monitor for improvement and deliver environmental reporting.
Operational focus
Physical and digital-process IoT improvement can support lean manufacturing goals. Using IoT systems often leads to steady process improvement, with traceable gains from operational efficiency and carbon, water, waste and energy reductions that can be matched to sustainability targets.
Physical improvement of manufacturing systems includes benefits in the movement of goods intra-factory, such as fewer and shorter distances traveled per part and unit of labor by organizing parts into correctly sized, flexible production cells, and less space required by physical inventory, processed and finished goods because customers receive orders when they are needed.
Process improvements in digital systems could include benefits from robotic process automation, which impact carbon, energy efficiency and other measures, as well as effective data governance, which affects management and process efficiency. IoT can also improve digital processes, such as the alignment of enterprise network system architecture with IT/OT device integration and planning, improved middleware and component system mapping, a renewed data catalog and opportunities to implement a common data model.
Digitalized reporting systems enable quick access for stakeholders in disparate internal and external organizations, creating opportunities for green supplier network alignment and improvement.
Emphasis on compliance
Many regulators and other stakeholders in the context of sustainable manufacturing goals, including customers, require trust, traceability and transparency in data. IoT can help deliver trustable, traceable and transparent data retention in a shared database system called a distributed ledger
A distributed ledger is a form of distributed database that permits manufacturing plant teams, customers and ecosystem stakeholders to have a single version history of the ledger, uniquely having separate informational, transactional and financial reporting characteristics. Further, such database systems can contain features that enable automations that trigger outcomes when thresholds are discovered in the data being gathered.
For example, a distributed ledger could hold the data that measures the output of an emissions stack for specific gasses, as well as all the operating data matched by timestamp to the plant output. Such distributed systems allow a regulator — or other stakeholder in a regulatory reporting role — to have a full copy of the entire database.
Distributed ledger IoT systems can be designed to record data from any sensors and systems that are important within the context of the relationship between the regulator and the operator, the customer and the supplier, or even the departments or singular equipment within a single facility. Distributed ledgers are a major class of technology that is expected to improve sustainable manufacturing through data availability, transactional transparency and automation, and reporting benefits.
Considerations for implementing IoT that supports sustainability
Implementing IoT technology comes with challenges when it comes to sustainable manufacturing. For example, capital improvement of processes and facilities presents cost-benefit evaluations that require exploration through effective modeling and strategic assessment of options. Modeling should include a scenario-driven assessment of goals and measures of planned outcomes in concrete terms and KPIs that address commitment and action from stakeholders, time to implement and potential for improvement.
Compliance with local, regional and national laws regarding building and fire codes is also relevant when considering manufacturing process physical system improvement.
Data governance is an important aspect of digitalization in sustainable manufacturing given that the quality of the data affects real-time performance modeling, operations maintenance improvement and reported outcomes for stakeholders.
Despite these challenges, IoT plays an important role as a key enabler for sustainable manufacturing.