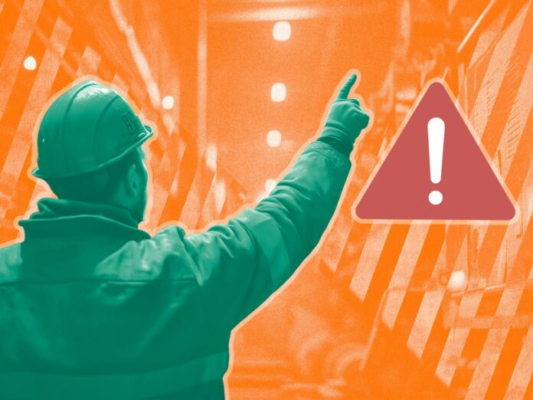

Owners, operators, engineers, and project managers working in industrial settings recognize the importance of performing maintenance regularly to reduce the total cost of ownership of their equipment and reduce downtime.
Instead of maintaining equipment reactively, it’s best to take a predictive maintenance approach so you can work proactively. This is why many facilities deploy IoT technology to streamline operations and complete predictive maintenance.
Industry professionals can identify potential equipment failures well before they happen through IoT-powered sensors and data analytics. This helps them avoid unnecessary downtime while boosting their operations’ efficiency. Shifting to IoT devices leads to cost savings and increased productivity in industrial settings.
Key Aspects of Internet of Things Devices in Industrial Settings
Install IoT sensors to gather information in real-time from all essential equipment, devices, and systems. Sensors will give you accurate details about how much energy a device is using, its temperature, vibration, and other crucial measurements. These details can help IoT devices alert you when predictive maintenance may be needed.
You can also use IoT devices to send information to other equipment, such as system status reports that appear on employees’ mobile devices or workstations. They also send commands to actuators based on how you’ve programmed them to respond, such as to turn off a machine that is running too hot.
The IoT system gives you continuous feedback on the state of your industrial operations. For example, installing IoT ultrasonic flow meters non-intrusively tells you how much volume is moving through pipes. They identify the temperature of fluids and their speed and are suitable for monitoring everything from high-pressure steam to low-viscosity fluids in the pipeline. You’ll get instant feedback if a system is not working according to specification.
Using IoT Devices to Bolster Predictive Maintenance
IoT devices provide many benefits when deployed to enhance predictive maintenance in industrial settings. They enable you to monitor conditions in your facility 24/7, even in harsh environments that would be dangerous for workers to inspect. With IoT devices gathering data on your behalf, you can free up workers to focus on more complex tasks.
By placing small IoT devices on your machinery, you gather vital information and then transmit it to a central location, such as your cloud server so anyone can access the data in real-time. This is useful when guiding technicians to a specific area or device for them to inspect and repair.
While it’s difficult for people to analyze the torrent of information on their own, you can apply machine learning algorithms to identify changing trends, such as minor variations in how a component vibrates or if the temperature is slowly falling or rising, indicating possible issues that need maintenance.
Use AI and machine learning along with IoT to help determine when machines are close to breaking down and failing and predictive maintenance may be needed. A proactive approach saves you time because you address problems while they’re still relatively small and easier to fix or replace. You can, therefore, avoid idling workers and disrupting your production schedule.
Deploying IoT Devices to Save Money and Work More Efficiently
Installing IoT devices in your industrial facility will help you understand what predictive maintenance tasks to do next, saving time and keeping your systems running more efficiently with less downtime.