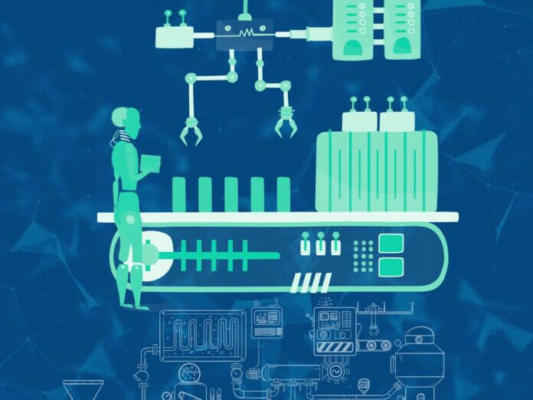

The integration of smart technologies has revolutionized modern industrial operations, offering unprecedented opportunities for efficiency and innovation. The IIoT, combined with cloud, AI, and machine learning, is revolutionizing operations and equipment management.
How IIoT is Shaping Industrial Operations
The IIoT represents a significant shift in how industrial companies monitor and manage their machinery. IIoT enables real-time equipment monitoring, replacing manual inspections with data-driven, proactive decision-making.
In practical terms, IIoT systems involve embedding sensors into industrial machines to collect data on parameters such as temperature, vibration, load, and energy consumption. Data is sent to central points for analysis, giving engineers a full view of equipment health.
The real power of IIoT lies in its ability to turn raw data into actionable insights. Analyzing trends helps predict failures, schedule maintenance optimally, and prevent costly unplanned downtime.
Unlocking the Benefits of IIoT for PCB Manufacturing
IIoT condition monitoring doesn’t just offer incremental improvements; it fundamentally changes how industrial companies operate. Here are some ways IIoT is unlocking new potentials in manufacturing:
- Data-driven decision-making: The continuous flow of data from IIoT sensors allows companies to make informed decisions based on real-time information rather than relying on historical data or estimates. This leads to more precise maintenance schedules, better resource allocation, and improved operational efficiency.
- Enhanced operational visibility: With IIoT, manufacturers gain unprecedented visibility into their operations. This visibility extends beyond just the status of individual machines to include overall production processes, enabling a more holistic approach to optimization and problem-solving.
- Reduced maintenance costs: One of the most significant benefits of IIoT is its impact on maintenance costs. Predicting failures allows companies to perform necessary maintenance, reducing repair frequency and spare parts inventory.
- Improved safety and compliance: IIoT systems can also monitor conditions that affect workplace safety and regulatory compliance. For instance, sensors can detect hazardous conditions such as excessive temperatures or toxic gas leaks, triggering alerts and automated responses that protect workers and ensure compliance with safety regulations.
Real-World Application
One of the most critical applications of IIoT in manufacturing is the monitoring of rotating equipment, such as pumps, motors, and compressors. These components are essential to many industrial processes, and their failure can result in significant downtime and financial loss.
In PCB manufacturing, for instance, vibration monitoring is crucial for maintaining the health of pumps used in the production process. Vibration sensors measure the frequency and amplitude of a pump’s vibration signature, allowing engineers to detect early signs of wear and tear. This proactive approach helps prevent equipment failures that could disrupt production and lead to defective products.
Case Study
Let’s explore a practical example of how Prylada implemented IIoT to monitor critical machinery.
The Challenge
A PCB manufacturer was struggling with the inefficiency of manual pump inspections. The maintenance team had to rely on visual checks and spreadsheets to track vibration levels, a process that was not only time-consuming but also prone to errors.
The Solution
The company decided to implement an IIoT-based condition monitoring system designed by Prylada. This system automated the entire process, from data collection to visualization. Here’s how it worked:
- Data collection: Sensors embedded in the pumps collected detailed vibration data.
- Data transmission: The data was aggregated by Prylada’s Probeberry Gateway and sent to an on-premises server via Ethernet.
- Data visualization: The data was then processed and displayed on a user-friendly dashboard, allowing engineers to monitor pump conditions in real time.
The result was a significant reduction in unplanned downtime and maintenance costs. The factory could now proactively address issues before they led to equipment failure, ensuring continuous operation and improving overall productivity.
IIoT Adoption
In the fast-paced world of PCB manufacturing, where production lines operate around the clock, unplanned downtime can lead to significant financial losses. The adoption of IIoT-based condition monitoring systems marks a shift from reactive to proactive maintenance strategies, ensuring that critical machinery remains operational and efficient.
By embracing IIoT, manufacturers not only enhance the reliability of their equipment but also unlock new opportunities for operational excellence and innovation. This technology-driven approach is essential for staying competitive in today’s industrial landscape, where efficiency, safety, and sustainability are paramount.